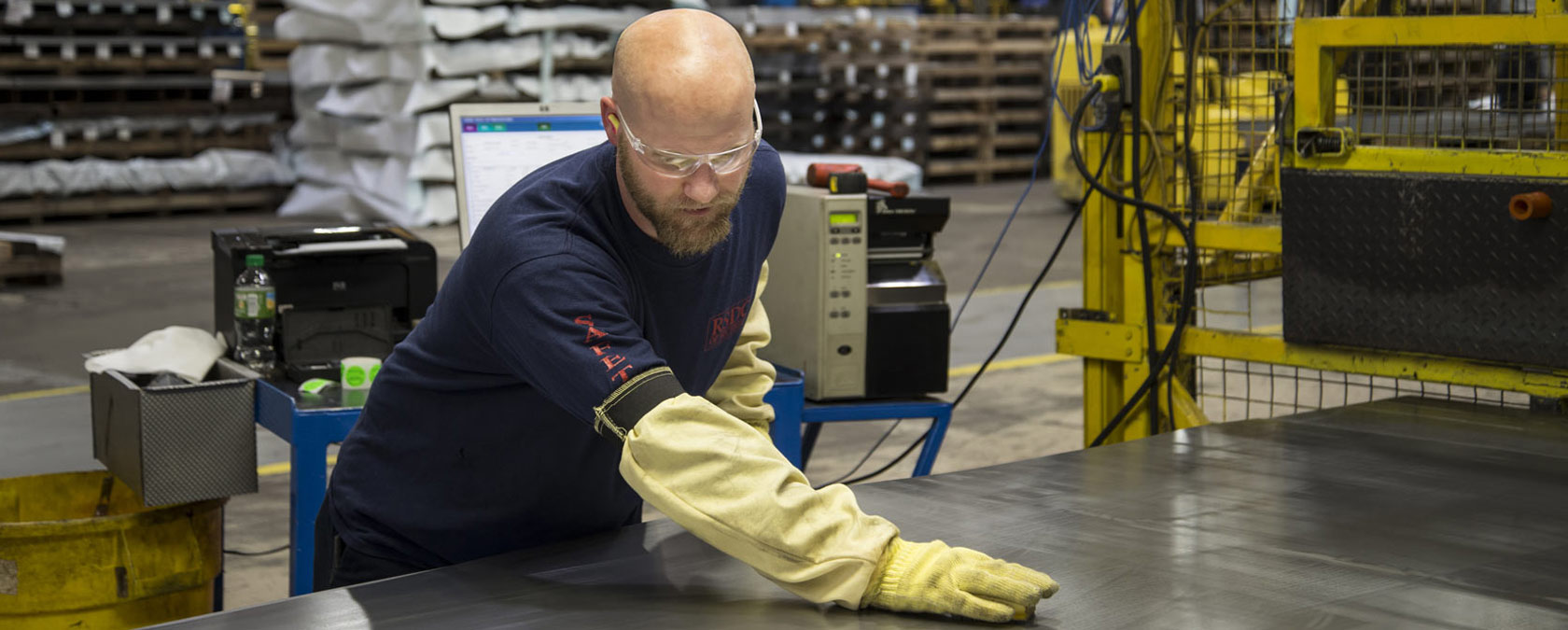
Blanking
Four industry leading, metal coil-fed blanking lines are at the core of RSDC. These four impressive lines feature process automation and optimal inspection capabilities to ensure the highest quality goods produced safely and efficiently.
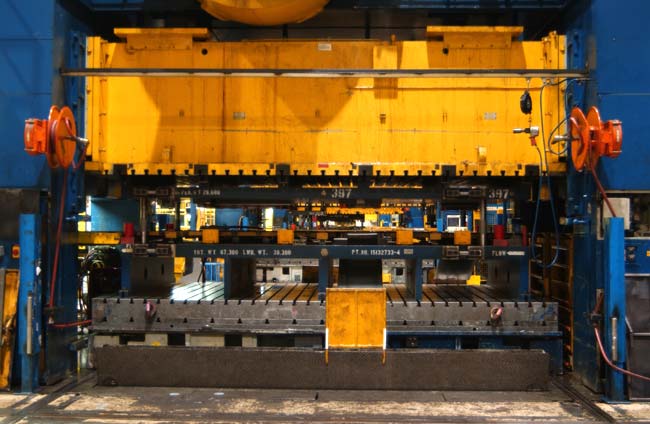
The advantages customers experience with RSDC’s blanking lines include:
- Automated processes to provide consistent and efficient production
- Feed forward capabilities to enable auto rejection of material pieces based on defect data communicated by the steel mills
- Dual inspection capabilities to ensure 100% top and bottom inspection
- Elevated inspection stations to provide better viewing and optimized inspection processes
- Automatic “one button” rejection to dispose of non-conforming pieces during inspection
- Rockwell software automates part recipe set up and part processing history to continually ensure best manufacturing practices
- Dual stacking system with four pilers to provide continual stacking without halting production
- Online packaging capabilities to ensure material is ready to ship off the line
RSDC’s blanking lines include three 800-ton exposed capable lines and one 600-ton unexposed press. The 800-ton press lines feature in-line leveling, high pressure hot water wash, top and bottom electrostatic oiling, and 100% top and bottom inspection. The 600-ton line features in-line leveling and hand-stacking of parts. Together, these four lines offer a combination of capabilities that are rare industry-wide, including:
- Crane loading with a capacity of up to 90,000 lbs. on all four lines
- Automated top and bottom coil loading on all four lines
- Press beds of 102 x 204 inches and 102 x 144 inches
- Up to 84-inch blanking
- 6 high leveler with 9 over 10 rolls and full-width intermediate rolls
- Sheet height of up to 53 inches with a 31-inch adjustable pass line
- Elevated inspections stations for better viewing and optimized inspection processes
- Piler unloading via crane or hi-lo
Blanking Line Specifications
The specifications for each of RSDC’s four blanking lines are described below.
Blanking Lines 1 & 2
- Material Type: Electrogalvanized, Hot Dipped, Galvanneal, Cold Rolled (class 1 & 2), Aluminum
- Steel Gauge: 0.5mm (0.02”) min to 2.3mm (0.09”) max
- Aluminum Gauge: 0.5mm (0.02”) min to 2.3mm (0.09”) max at 40 kpsi
- Coil Weight: 40.8 metric tons (90,000 lbs.)
- Steel Width: 457mm (18”) min to 1930mm (76”) max
- Aluminum Width: 609mm (24”) min to 1930mm (76”) max
- Sheet Length: 305mm (12”) min to 4013mm (158”) max
- Feed Accuracy: +/- 0.25mm (0.10”) set value
- Electrostatic Oiling: 25 – 300mg/sq. ft. (two-sided)
Blanking Line 3
- Material Type: Electrogalvanized, Hot Dipped, Galvanneal, Cold Rolled (class 1 & 2), Aluminum
- Material Gauge: 0.5mm (0.02”) min to 2.3mm (0.09”) max
- Coil Weight: 40.8 metric tons (90,000 lbs.)
- Coil Width: 457mm (18”) min to 2134mm (84”) max
- Sheet Length: 305mm (12”) min to 4013mm (158”) max
- Feed Accuracy: +/- 0.25mm (0.10”) set value
- Electrostatic Oiling: 25 – 300 mg/sq. ft. (two-sided)
Blanking Line 4
- Material Type: Hot Dipped, Galvanneal, Cold Rolled (class 2), Aluminum
- Material Gauge: 0.5mm (0.02”) min to 3.47mm (0.13”) max
- Coil Weight: 40.8 metric tons (90,000 lbs.)
- Coil Width: 457mm (18”) min to 1930mm (76”) max
- Sheet Length: Reviewed case-by-case; hand stacking only
- Feed Accuracy: +/- 0.25mm (0.10”) set value
- Electrostatic Oiling: N/A
Four Blanking Units:
- High pressure hot water wash and electrostatic oiling
- Two-sided inspection capabilities
- Inline leveling
- Feed forward capabilities
- Capacity of running up to 60 strokes per minute on the blanking lines and 90 strokes per minute on the CTL
*Shut Height for all: 1270 mm (50″)
*Pass Line Height for all: 762mm (30″)
*Min/Max coil ID 24″-24″ and Min/Max coil OD 36″-80″